COVID-19 Digital Strategies Guide
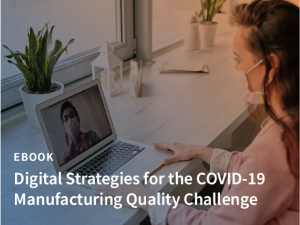
COVID-19 Challenges
The COVID-19 pandemic has created urgent challenges for every business. While some challenges are unique, many are common across different industries, including:
- Ensuring the health and safety of employees, suppliers and customers
- Managing a distributed and stressed workforce
- Reacting to variations and uncertainties in demand
- Managing new supply chain challenges
- Sifting through mountains of new information and misinformation
- Maintaining a constant and positive flow of communication
Manufacturing, Operations and Quality executives are scrambling to adapt and lead during this unprecedented period. Now, more than ever, they are eager to learn from their peers and share best practices. The more visionary leaders are seeing this not only for the crisis that it is, but also for the opportunities that are emerging.
Emerging Opportunities
In the words of Winston Churchill, “never let a good crisis go to waste”
Many companies are finding opportunities emerge from crisis. For some, their products are in higher demand than ever. Others are embracing and redefining work-from-home policies. Still others are making use of their factory downtime to retool processes and systems. In fact, the most forward-thinking industry leaders are using this time to accelerate their digital transformation initiatives by automating and streamlining manufacturing quality processes to increase efficiencies, improve quality, and drive growth.
There are multiple forces driving this digital acceleration:
Need to Evolve Manual Processes
Any process that required passing around paper demanded an immediate overhaul once employees started working from home as a result of COVID-19.
Need to Evolve In-Person Activities
Any process requiring in-person interaction also required rethinking due to stay-at-home orders. Audits are now virtual, making it mandatory to have a digital system of record for every audited process.
Need to Define and Deploy Quickly
COVID-19 has introduced the need to rapidly deploy new processes and improve existing ones across the enterprise. Digital tools can accelerate & reduce the cost of these efforts with automated workflows & real-time reporting
The argument to accelerate digital transformation has never been stronger. This guide highlights some of the ways manufacturing, operations and quality executives are advancing their digital agendas in response to the COVID-19 pandemic, but also with an eye to the future.
Advantages of Digital
The advantages of going digital are well established and include:
Better Quality Data
Digital data is easier to store, edit, access and share. It can be backed up for better retention. It can be secured and privacy-protected to reduce risk.
Faster, Leaner Processes
Digital processes automate time-consuming manual workflows, resulting in faster and more streamlined operations that eliminate waste and increase productivity.
Quality Compliance
Digital processes make it easier to ensure consistent, compliant execution. Process deviations can be automatically flagged, reported and escalated.
Easier Auditing
Digital processes simplify audits by having all process-related information in one place. Digital signatures and audit logs provide a clear record of activity and change history.
Increased Accountability
Digitization enables real-time reporting of key process metrics, making it easier to track performance vs. targets, and driving accountability to results.
Improved Decision Making
Digital data can be normalized, aggregated and analyzed for trends, resulting in new insights and better decision making.
New Value Creation
Digital transformation can lead to entirely new business models and value streams that drive long-term growth, create competitive advantage and boost profitability.
Three Phases of Digital Evolution
There are three distinct levels of digital evolution that are worth considering before beginning any digital project. Each level depends on the one below it.
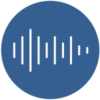
Digitization – converting data from analog to digital. Ink on paper is replaced by electronic bits in a computer. Digitization unlocks data, making it available for aggregation and analysis.
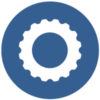
Digitalization – converting processes from manual to digital. Workflows are automated, approvals are granted electronically, process deviations are instantly flagged, & performance metrics are tracked in real-time. Digitalization leans out operations, while improving quality and compliance.
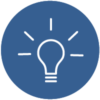
Digital Transformation – transforming entire businesses and operations to create new value streams & business models. Digital transformation replaces or enhances traditional products and services with something entirely new, just as Netflix reinvented entertainment and Amazon reinvented the shopping experience.
It’s important to pursue every digital project with a vision toward the future. Even the simplest digitization project has ramifications down the road because it defines what data will be captured and how it will be formatted.
Creating New Processes
COVID-19 brings unprecedented challenges that have driven the need for new processes. To address these challenges, SIMCO and our customers have raced to create and digitize new processes, including:
- Planning and executing virtual audits – both internal and external
- Tracking the real-time readiness and capacity of critical suppliers
- Tracking and sourcing Personal Protective Equipment (PPE) and cleaning supplies
- Monitoring employee self-reporting and daily health checks
- Scheduling deep cleaning of workspaces, vehicles and equipment
- Classifying employees as essential or non-essential and providing appropriate COVID-19 related training and communication to each group
When implementing new processes under duress, there may be pressure to go with quick, manual solutions. But if the process is mission-critical or likely to persist for more than a few months, taking the time to plan and implement a digital strategy yields both short and long term results.
Update Existing Processes
Many existing quality processes have had to evolve in response to COVID-19’s impact on the workforce. SIMCO and our manufacturing customers have been investing in some of the following digital enhancements:
Eliminating Paper
Processes that previously involved paper-based record-keeping are no longer feasible with many employees working from home. Examples include:
- Receiving, inspecting and processing paper certificates from suppliers
- Documenting changes to service specifications (i.e., maintenance intervals)
- Documenting changes to equipment status (i.e., active/inactive)
- Assessing the impact of non-conformances (i.e., calibration failures)
Sharing Equipment
Gaining enterprise-wide visibility of equipment and its usage creates opportunities for sharing, thus reducing spending on new equipment. This is especially valuable in times of downsizing and site consolidation.
Changing Service Requirements
Many of our customers have needed to make changes to services performed, including:
- Moving onsite services to pickup & delivery
- Moving pickup & delivery to onsite
- Adding new equipment cleaning requirements
- Adding new service provider personnel requirements, etc.
Leveraging digital systems to document and track these changes helps to ensure clear communication among all stakeholders and manage expectations.
Coordinating Service Scheduling
Coordinating calibration and preventive maintenance schedules to minimize downtime for essential operations or to take advantage of downtime for non-essential operations.
Empowering Remote Workers
Stay-at-home orders have forced a dramatic increase in the number of remote workers and a dramatic decrease in travel and in-person meetings. Every company has had to cope with this new normal and many are considering how to embrace and empower a distributed workforce. Digital plays a critical role. Remote employees need all the same capabilities that are available in the office, plus new capabilities to collaborate and communicate with distributed teams. Video conferencing, screen sharing, messaging, and document sharing applications have become vital productivity enhancers, while paper copiers and printers sit idle.
For mission-critical enterprise processes, modern cloud-based solutions offer several advantages for a distributed workforce:
- Easier remote access (VPN not required)
- Easier to extend access to non-employees (i.e., customers, partners, auditors)
- Outsourced datacenter that does not require additional/onsite resources and personnel
- Secure backups and automated updates that do not burden IT resources or require onsite activity
The COVID-19 pandemic has provided companies with a glimpse into a future that embraces a more distributed and digitally enabled workforce.
Digitally Transforming Manufacturing Quality
In addition to addressing the immediate challenges created by COVID-19, leading manufacturers are embracing the opportunity to advance their digital agenda. With advanced manufacturing quality software from SIMCO, the world’s largest lives-at-stake manufacturers are automating, streamlining and reducing waste across a broad suite of processes including:
- Calibration
- Preventive Maintenance
- Work Requests
- Asset Tracking
- Inventory Management
- Parts Management
- Tool Crib Management
- Non-Conformance Analysis
- Equipment Enrollment
- Validation Management
- Employee Training & Certifications
- Production Testing
- Use Trace
- Partner Management
- Audit Scheduling & Management
- Review/Approve Vendor Work
- Facility Certifications
- EH&S Task Compliance
- Equipment Downtime Tracking
- Radiation Exposure Tracking
SIMCO’s CERDAAC is a secure, cloud-based software platform widely used to automate the above processes and more. To learn how you can digitally transform your manufacturing quality processes, email us at hello@simco.com or give us a call at 1-866-299-6029.
Summary
While the COVID-19 pandemic has presented significant new challenges, digital technology can help you meet these new challenges and provide many lasting improvements to your operations. Industry leaders are finding the opportunity during this crisis to embrace digital transformation strategies that help their organizations streamline and automate processes, reduce costs, and enable a remote workforce that can work productively and safely.
To learn more about how SIMCO can help you in your digital transformation journey, schedule a demo. If you have suggestions for other best practices that can be shared in future versions of this guide, please email us at hello@simco.com. Thank you in advance for your contribution!